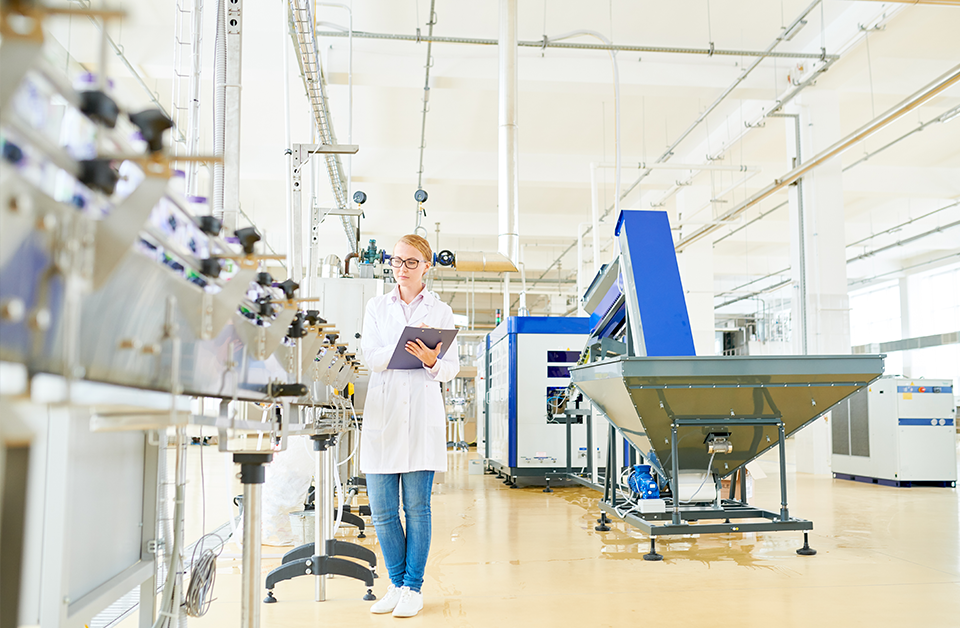
Minimize Microbiological Contamination in Dairy Separation Systems
Maintaining hygienic conditions and complying with product safety regulations are crucial for dairy processing plants globally. Due to the complexities of dairy operations, plants must adhere to strict guidelines and procedures to maintain product quality and manage operational risk. Microbiological contamination is an important consideration as it can result in increased cleaning requirements, decreased productivity or contaminated final products. From the expense of membrane replacements to the cost of an unscheduled plant shutdown, minimizing contamination is a high priority for plant operators and managers. Proper operating and cleaning procedures and choosing high-quality separation solutions are key to maintaining sanitary conditions and eliminating contamination.
How does Microbiological Contamination Happen?
Microbiological growth readily occurs in our natural environment when a microbe gets exposed to the proper conditions, which include temperature, pH, water, oxygen, pressure and a nutrient source. Microbiological contamination refers to the non-intended introduction of bacteria, yeast, mold or other elements to a product or surface. Food products that are rich in nutrients are particularly susceptible to contamination.
Because of the complexity of the dairy process and the propensity for microbiological growth, given the operating conditions, it is critical to use proper procedures and separation solutions. Separation of the incoming milk stream into valuable products is at the heart of every dairy process. Processing plants use microfiltration (MF), ultrafiltration (UF), nanofiltration (NF) and reverse osmosis (RO) membrane separation technology extensively to fractionate and concentrate milk and whey streams as well as concentrate additional co-product streams that are further processed into finished goods or polished for reuse water. An example of the complexity of the process is shown below in Figure 1.
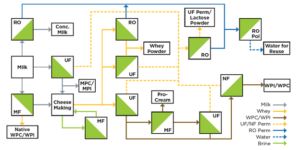
Figure 1: Example of a Dairy Process
MPC = Milk protein concentrate, MPI = milk protein isolate, WPI = whey protein isolate, WPC = whey protein concentrate
Choosing the best membrane solution and optimizing the cleaning and sanitation process is important. Some membrane solutions, such as Reverse Osmosis, can be more vulnerable due to blistering, which increases the risk of microbiological growth. Blistering typically occurs when the glue line is not entirely sealed during the membrane manufacturing process and separation occurs, allowing a small “bubble” to form. Although tiny, these imperfections in the glue line can trap products under the surface of the membrane, causing an unsanitary spot where bacteria and microbiological growth can thrive.
Combatting Microbiological Growth – What Can You Do?
Under normal operating conditions, microbiological contamination issues can be mitigated by maintaining proper cleaning and sanitation (C&S) procedures during operation, including regular Clean-In-Place (CIP) cleaning of membranes. However, the best approach is carefully choosing the best membrane solution. Dairy processing plants should collaborate with their membrane providers and C&S suppliers to develop a dairy separation strategy and select the most appropriate combination of technologies to achieve their safety and quality goals.
How can Solecta help?
Solecta’s spiral wound, polymeric, blister-resistant membrane technology improves efficiency, reduces operating costs, increases productivity and decreases contamination risk. Our consultative and analytical approach leverages chemistry and process expertise to deliver reliable data and critical insights to maximize gains during a customer’s separation processes. Our team brings deep industry expertise and works with our clients to define and deliver solutions with maximum value.
Click here to discover what dairy companies are doing to optimize the safety and hygiene of their operations, maximize productivity and create value.
Related Resources in the Knowledge Hub
Let’s Keep in Touch
Follow Solecta on LinkedIn and join our mailing list to keep up with our latest news.
Explore the Possibilities
Our team of application engineers and domain experts understands your industry’s unique challenges. (They’re also eager to solve them.)