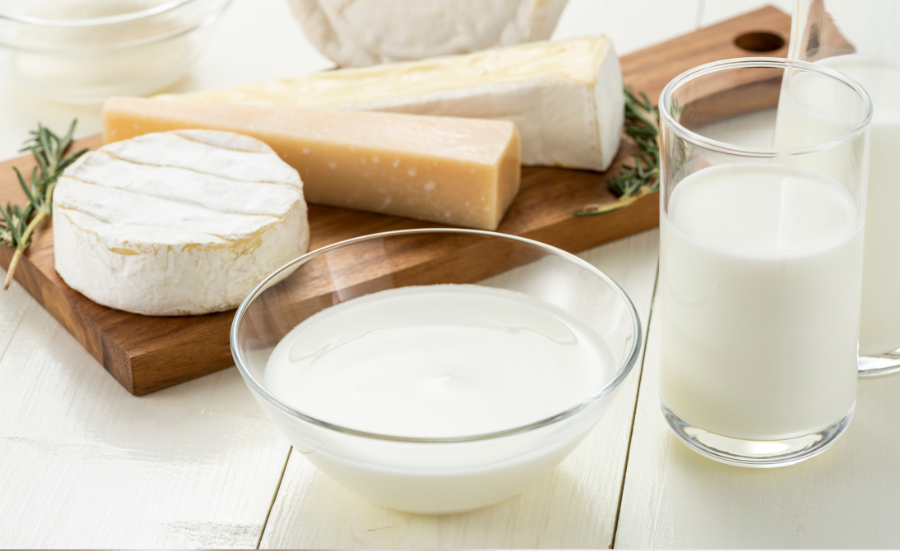
Cut the Costs, Not the Quality: Cost-Effective Membrane Separation Solutions for Dairy Processors
In today’s competitive dairy industry, processors are constantly on the lookout for innovative solutions that can help them optimize their operations while reducing overall costs. Maintaining the balance between product quality and operational efficiency is critical as margins become slimmer and the demand for diverse dairy products continues to grow. Progressive processors are seeking advanced technology and solutions that not only increase their yields and productivity but also reduce their capital investment, operating and maintenance costs. Membrane separation is one solution, streamlining production and delivering superior products at a lower cost while maximizing productivity, minimizing waste and driving profitability. In this blog, we’ll discuss their reliable performance, high recovery rates, and low fouling propensity – benefits that ensure minimal downtime and maximal productivity for processors eager to stay ahead of the curve. So, grab a glass of milk and join us on this exciting journey towards more sustainable and economically viable dairy production.
Streamlined Capital Investment
The use of membrane separation solutions in the dairy industry has become increasingly popular due to technological advancements that have made membrane technology affordable and scalable. These solutions can be customized to fit the needs and budgets of dairy processors, whether they are large-scale facilities or small local producers. As technology progresses, membrane separation allows processors to achieve optimal performance by customizing their filtration systems. Whether it’s the desired throughput, separation efficiency or product quality, the membrane system can be fine-tuned to meet their specific requirements. This level of customization ensures that their capital investment is strategically aligned with production goals, minimizing unnecessary expenses and optimizing resource allocation. Additionally, the scalability of these systems allows for seamless expansion as production demands increase, future-proofing their operations and facilitating continuous growth. This approach enables processors to reap the maximum benefits from their investment, ensuring long-term sustainability and growth.
Operating Costs
The success of dairy processing plants heavily relies on minimizing operating costs, and solutions like membrane separation help to achieve this. Membrane technology allows processors to efficiently separate valuable components with a high recovery rate, which minimizes product loss and reduces waste and disposal costs. These benefits have a direct, positive impact on the processor’s bottom line.
A key advantage of membrane separation technology lies in its energy efficiency. Compared to more traditional separation or concentration processes, membrane systems require less power, resulting in lower utility bills and reduced operating costs. By optimizing energy consumption, dairy processors can realize substantial savings while maintaining the high-quality standards of their products. This energy efficiency not only contributes to cost savings but also aligns with sustainability goals, reducing the environmental footprint of dairy processing operations.
The compact design of membrane systems offers additional cost advantages to dairy processors. These space-saving solutions minimize the need for extensive construction and facility maintenance, reducing capital investment and ongoing operational expenses. Furthermore, efficiently utilizing space allows for streamlined workflows, optimizing resource allocation and minimizing energy and water consumption. This holistic approach to cost reduction makes membrane separation solutions attractive for dairy processors seeking to improve their financial viability.
Maintenance Costs
Regular maintenance serves as the cornerstone of a well-functioning membrane separation system. These systems require periodic attention to uphold their efficiency and durability. To prevent small issues from growing into substantial problems, dairy processors should adopt a proactive maintenance strategy. This approach focuses on preventative measures to detect and address potential problems before they cause significant disruptions.
Automated monitoring and control systems are invaluable assets in proactive maintenance. These systems continuously monitor key parameters, such as pressure differentials, flow rates and separation efficiency. Detecting early signs of performance degradation triggers alarms or alerts, providing dairy processors with prompt notifications to take corrective action. This proactive intervention allows processors to promptly tackle emerging issues, preventing them from escalating into costly breakdowns or compromising the overall productivity of the system.
Routine inspections, cleaning, and timely replacement of worn-out components are essential maintenance tasks that dairy processors should prioritize. By conducting these activities diligently, processors can extend the lifespan of their membranes, optimizing their performance and minimizing unexpected downtime. Proactive maintenance not only ensures the smooth operation of the equipment but also acts as a shield against unforeseen breakdowns, significantly reducing repair costs and maximizing the return on investment.
Cutting-Edge Membrane Separation Solutions
Advancements in membrane technology have led to the development of low-fouling membranes with extended lifespans. Fouling, the accumulation of deposits on the membrane surface, can drastically reduce membrane efficiency and performance. Low-fouling membranes are designed to repel particles and foulants, reducing the frequency of cleaning cycles and maintenance interventions. This translates to extended membrane lifespan, reduced costs and increased operational uptime. These advancements have transformed the landscape of dairy processing, providing processors with reliable and long-lasting solutions that maximize efficiency.
Hybrid membrane systems have emerged as a powerful approach to improve separation efficiency in dairy processing. By combining multiple filtration techniques, such as microfiltration, ultrafiltration, nanofiltration or reverse osmosis, each targeting a specific molecular size or property, processors can achieve enhanced separation performance and tailored product quality. The synergistic effects of combining multiple membranes result in improved system efficiency, higher product yields and reduced waste generation. This innovative approach enhances the competitiveness and profitability of operations by maximizing the efficiency of separation and delivering high-quality products.
In conclusion, membrane separation is a cost-effective and efficient solution for dairy processing offering manufacturers a comprehensive and sustainable solution. Not only do they streamline production and enhance product quality, but they also provide significant cost savings. By reducing energy consumption, reclaiming valuable byproducts, and minimizing waste production, membrane separation technologies positively impact the bottom line and contribute to a more sustainable, eco-friendly operation. With its reliable performance, high recovery rates, and low fouling propensity, this technology has become a key asset in maximizing efficiency and profitability. As the demand for dairy products evolves and grows, employing membrane separation solutions offers a competitive advantage for businesses looking to expand and meet market demands.
Related Resources in the Knowledge Hub
Let’s Keep in Touch
Follow Solecta on LinkedIn and join our mailing list to keep up with our latest news.
Explore the Possibilities
Our team of application engineers and domain experts understands your industry’s unique challenges. (They’re also eager to solve them.)