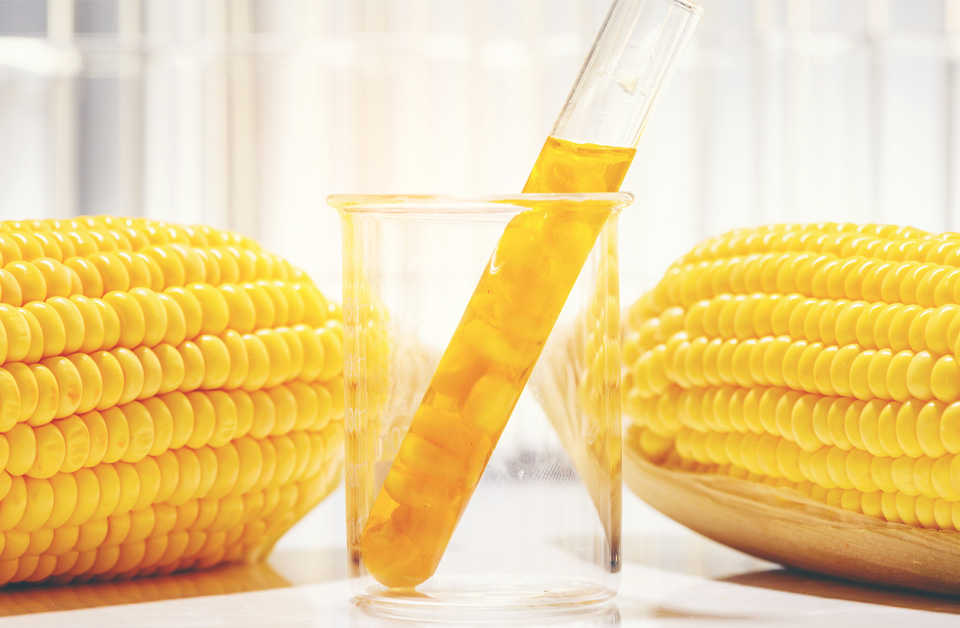
Membrane Separation Technology: A Game Changer in Precision Fermentation Applications
Executive Summary
Membrane separation technology has become an increasingly popular method for improving downstream operations in fermentation manufacturing. This technology is pushing the boundaries of product innovation across various sectors through its energy efficiency, selectivity and scalability. By employing this technology, the efficiency and effectiveness of the fermentation process can be significantly enhanced, reducing production costs and improving product quality. As research into new materials and techniques continues, we expect membrane separation capabilities to play an even more significant role in supporting sustainable future production methods. Its versatility allows for seamless integration into various industries, making it a key tool for advancing scientific research and maintaining competitiveness in the market. As we explore new frontiers within biotechnology and chemical engineering, membrane separation technology will undoubtedly remain at the forefront of groundbreaking solutions to overcoming challenges in precision fermentation.
In the evolving world of biotechnology, precision fermentation has emerged as a leading method of producing high-value compounds with unparalleled control and efficiency. This rapidly growing field uses microorganisms to produce products from food ingredients to pharmaceuticals. According to a recently published Polaris market research report, the global market was USD 1.30 Billion in 2021 and is expected to reach USD 37.35 Billion by 2030, growing at a CAGR of 48.3% during the forecast period [1]. A key enabler of this process is membrane separation, which has become a cornerstone for ensuring successful outcomes in a wide range of applications. As the demand for sustainable and clean production processes increases, it provides a safe, efficient and cost-effective solution for downstream processing in fermentation. Separating and purifying product streams helps improve the yield and quality of precision fermentation products In this blog, we’ll explore the world of membrane separation and its importance in optimizing precision fermentation processes. By delving into the unique interplay between these two innovative technologies, we can better understand how they are redefining boundaries and shaping the future of bio-based production, with the potential to transform industries and enhance our daily lives. Join us on this exciting journey of discovery!
The Role of Membrane Separation in Precision Fermentation
Precision fermentation is a bioengineering process that harnesses microorganisms’ ability to produce specific target molecules. These molecules can be proteins, enzymes or other metabolites with valuable applications in pharmaceuticals, food and beverages, textiles and more. Membrane separation comes into play during the separation, purification and concentration steps of producing these products, ultimately leading to a more cost-effective and efficient downstream process.
One major advantage of membrane separation technology is its high selectivity, enabling manufacturers to focus on specific molecules or particles, resulting in purified products. For instance, separating proteins from lipids and carbohydrates enhances the purity of the final product, ultimately impacting its quality and yield. Moreover, they are low-energy processes, unlike traditional downstream processing methods like centrifugation and chromatography, which incur high energy costs.
Membrane separation is an excellent choice for large-scale fermentation manufacturing because it can be easily scaled up. Membranes can handle large volumes of products while maintaining a high level of selectivity and purity, ensuring that manufacturers can produce high-quality products and increase their production capacity without sacrificing the quality of their products.
The choice of membrane separation process depends on the size and type of the molecules that need to be separated. Some of the most common processes include:
Microfiltration (MF) separates and concentrates microorganisms and isolates desired components from contaminants, such as cell debris and unconverted substrate, ensuring higher purity and quality of the end products and efficient downstream processing. This process is used for applications such as cell harvesting, biomass separation, product purification, clarification of culture broth and removal of cell debris.
Ultrafiltration (UF) separates and concentrates desired components, such as proteins, enzymes and other biomolecules. This helps maintain optimal conditions for microbial activity, ensures accurate product formation, and improves the bioprocess’ overall efficiency and productivity. This process is utilized in biotechnology, food and beverage, and pharmaceutical industries to purify and concentrate complex mixtures.
Nanofiltration (NF) separates and purifies specific components such as proteins, amino acids and sugars. The purified components are used for various applications such as food and beverage production, biopharmaceuticals and nutraceuticals.
Reverse Osmosis (RO) separates and concentrates valuable components such as proteins, nutrients and other biomolecules. The process produces high-quality and purified substances for various applications such as pharmaceuticals, nutraceuticals and specialty chemicals.
Different approaches work on varying pore sizes to effectively separate components based on their molecular size and charge. Membrane separation is a valuable tool that helps improve the yield, purity, and sustainability of precision fermentation processes.
Benefits of Membrane Separation
Membrane separation offers multiple advantages over conventional purification methods. Some notable benefits include:
- Energy Efficiency: Membrane processes are typically less energy-intensive than traditional methods since they do not require heating or cooling steps
- Selectivity: The ability to control membrane pore size allows for the precise separation of target molecules based on size or charge, reducing contamination risks
- Scalability: Membranes can be designed to handle varying production levels and easily integrated into existing manufacturing systems
- Environmental Friendliness: As a clean technology, membranes are more selective, thus potentially generating less waste than other conventional methods
- Cost-effectiveness: When the lifespan of membranes is maximized, they are a very cost-effective means to separate and purify process streams
Advancements in Membrane Separation and Precision Fermentation Technology
Innovations in precision fermentation have led to a growing need for high-performance and cost-effective membranes with enhanced fouling resistance. To meet these demands, researchers are exploring novel materials and processes like nano-enhanced membranes, self-cleaning membranes, and even the integration of machine learning algorithms to optimize membrane performance.
Manufacturers are increasingly using newer methods, such as membrane adsorption and membrane distillation. Membrane adsorption is a process that uses a porous membrane to adsorb specific molecules or particles. In contrast, membrane distillation uses a semi-permeable membrane to separate liquids based on their vapor pressure. These newer methods are beneficial for separating large molecules, such as proteins, and can help improve product quality and yield.
In conclusion, the precision fermentation market has experienced remarkable growth in recent years, driven by increased demand for tailored and sustainable products. As a key unit operation of the manufacturing process, membrane separation has proven to be instrumental in achieving high efficiency and purity during the fermentation process. Not only does it contribute to waste reduction and energy savings, but it also supports the development of novel products with enhanced functionalities. As research into new materials and techniques continues, we can expect membrane separation technology to play an even more significant role in supporting sustainable future production methods. The ease of changing membrane configurations allows for seamless integration into various industries, making it a key tool for advancing scientific research and maintaining competitiveness in the market. The precision fermentation market is growing, and the use of membranes will contribute to its full potential, benefiting both industry applications and consumers. The future looks bright for both precision fermentation and membrane separation as we work together to optimize the way we produce food, pharmaceuticals and other essential products.
How can Solecta help?
Solecta’s spiral wound polymeric membrane separation technology improves efficiency, reduces operating costs and increases productivity. Our consultative and analytical approach leverages chemistry and process expertise to deliver reliable data and critical insights to maximize gains during a customer’s separation processes. Our team brings deep industry expertise and works with our clients to define and deliver solutions with maximum value.
[1] Precision Fermentation Market Share, Size, Trends, Industry Analysis Report, By Microbe (Yeast, Algae, Fungi, Bacteria); By Application (Dairy Alternatives, Meat & Seafood, Egg Alternatives, Others); By Ingredient; By Region; Segment Forecast, 2022 – 2030″ published by Polaris Market Research.
Related Resources in the Knowledge Hub
Let’s Keep in Touch
Follow Solecta on LinkedIn and join our mailing list to keep up with our latest news.
Explore the Possibilities
Our team of application engineers and domain experts understands your industry’s unique challenges. (They’re also eager to solve them.)