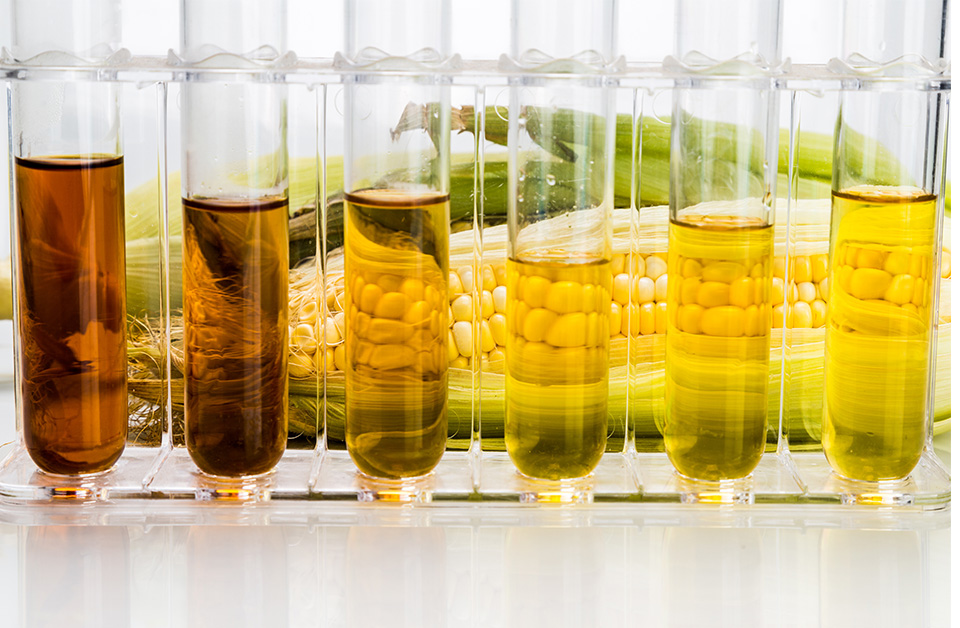
Selecting the Right Nanofiltration Solution to Increase Purity and Productivity in Dextrose Manufacturing
Nanofiltration (NF) is an important membrane filtration process that is gaining prominence in sugar and sweetener production due to its ability to separate mono-saccharides (DP1) from di-saccharides (DP2). With the variety of NF solutions available, dextrose manufacturers should be mindful of key parameters such as molecular weight cut-off, membrane flux and operating pressure to ensure optimal performance, quality and value delivery.
Below are a few key factors for dextrose manufacturers to consider when selecting the right NF solution.
- Feed stream composition: The feed stream’s concentration and impurity levels affects the available solutions. For example, if the feed stream contains significant enough impurities from upstream processes, a solution other than NF may be more practical. Another consideration is the impact of the concentration and consistency from incoming DP1 and DP2.
- Operating conditions: Different conditions such as pH, temperature and pressure can affect the performance of NF membranes. It’s important to select a membrane that can withstand the process’s specific operating conditions since many upstream processes operate at elevated temperatures.
- Product quality requirements: The higher the purity required, the “tighter” the NF solution will typically need to be to reject higher molecular weight sugars. However, suppose the finished product purity is not as critical. In that case, a membrane with a lower rejection rate and higher molecular weight cut-off may be more appropriate to hit target purity while also maximizing productivity.
- Flow rate and recovery: NF membranes with a higher flow rate and recovery rate can increase productivity and reduce costs. However, it’s important to balance this with the product quality requirements and the specific operating conditions of the purification process.
- Membrane fouling: Fouling can significantly affect the performance of the NF system. Selecting a membrane resistant to fouling that can easily be cleaned and maintained throughout several cleaning cycles is vital.
- Durability and longevity: Higher operating temperatures typical in the dextrose processing environment will cause a decrease in lifetime over processes that operate at lower temperatures. Membrane chemistry development is important to maximize performance and lifetime.
- Product availability: Considering today’s increasingly constrained supply chain, it is essential to understand a vendor’s performance with product lead times, on-time delivery and inventory levels. These variables are significant in helping ensure that adequate supply is available to support normal operations and unplanned disruptions that cause system failures.
Selecting the right nanofiltration solution is important for dextrose manufacturers to increase purity and productivity. By considering key factors such as feed stream composition, operating conditions, product quality requirements, flow rate and recovery, membrane fouling, durability and longevity and product availability, manufacturers can make the best choice for their needs. Manufacturers can ensure consistent performance, quality and value delivery with the right NF solution.
Once the appropriate membrane is selected, it’s important to ensure proper installation, maintenance, and cleaning of the system to maximize performance. Regular monitoring and data collection of key performance indicators (KPIs) such as flux, purity, and/or rejection and recovery can help identify potential problems and optimize performance. To ensure optimal results and help prevent issues, processors should request ongoing support from their suppliers, including troubleshooting, training and continuous improvement.
Solecta provides world-class membrane separation solutions to maximize efficiency and increase profitability for our clients. Our membrane solutions provide higher selectivity, energy efficiency and scalability, which helps our clients achieve better purity, concentration and recovery in their dextrose production. By leveraging our deep and broad application expertise, we help ensure our clients’ processes are optimized to deliver profitable results.
Success Story – Improving Purity and Increasing Productivity with a Dextrose Processor
A dextrose processor was experiencing quality issues and longer lead times from one of their NF suppliers, so they turned to Solecta for a solution. Solecta worked with this client to innovate a new solution that improved quality (through increasing purity to >99.5%) and increased productivity, achieving ~2% higher flow rates through the first three months of operation. This solution equates to as much as $1.6MM in additional productivity across all their NF systems!
Related Resources in the Knowledge Hub
Let’s Keep in Touch
Follow Solecta on LinkedIn and join our mailing list to keep up with our latest news.
Explore the Possibilities
Our team of application engineers and domain experts understands your industry’s unique challenges. (They’re also eager to solve them.)