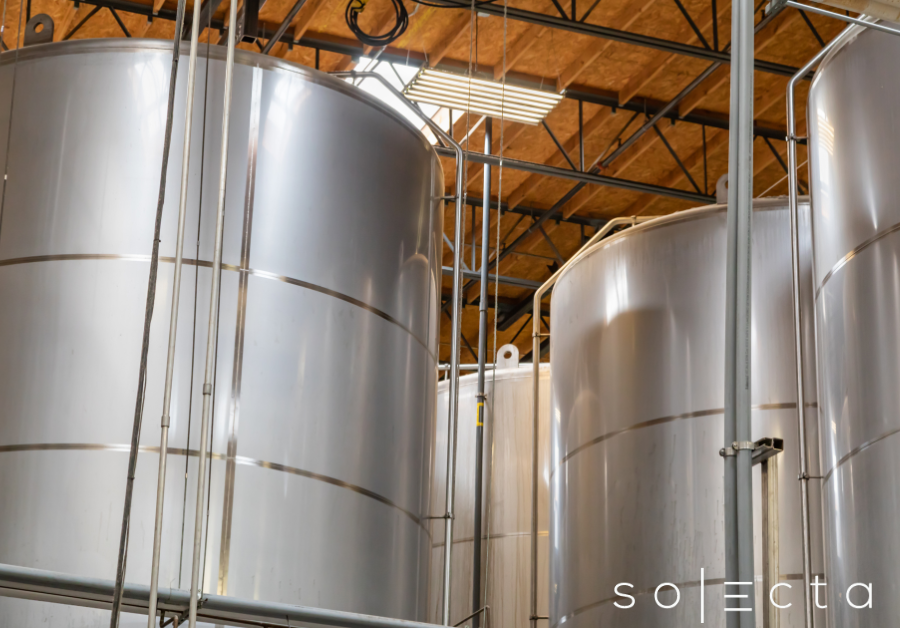
Sustainable Chemistry: How Fermentation and Membrane Filtration Drive the Future of Green Manufacturing
As companies increasingly seek sustainable alternatives for producing everyday molecules, fermentation has emerged as a key technology for producing renewable products. One area where fermentation is making significant strides is in the replacement of petroleum-based chemicals with bio-based small molecules such as 1,3-propanediol (PDO), 2,3-butanediol (BDO), and furan dicarboxylic methyl ester (FDME). These fermentation-derived chemical building blocks are becoming increasingly essential as companies seek to reduce their environmental footprint. However, a significant challenge in fermentation processes lies in downstream processing – specifically, the removal of unwanted contaminants and the production of a consistent, high-quality product that meets the market needs. This is where membrane filtration plays a crucial role.
The Fermentation Process
The production of PDO, BDO, and FDME via fermentation involves several critical steps to ensure the successful synthesis, purification, and functionality of the final product. The process begins with selecting the appropriate microorganism capable of producing the desired molecule, followed by preparing a fermentation medium containing the necessary nutrients for microbial growth and target molecule production. Once the medium is sterilized to prevent contamination, inoculation and controlled fermentation processes can begin.
Efficient harvesting of the final product is essential to meet quality and yield targets. The first step involves separating microbial cells from the fermentation broth using filtration or centrifugation. The subsequent steps involve clarification to remove cell debris and impurities, concentration to increase the final product’s concentration, and finally, purification to achieve the desired product quality. Optimizing each step is critical to achieving high quality and yield.
The Advantages of Membrane Filtration
Membrane filtration has become an integral part of downstream processing in fermentation. Whether the goal is to clarify the product, remove impurities, or concentrate and purify the final product, a combination of microfiltration (MF), ultrafiltration (UF), and nanofiltration (NF) enables producers to consistently meet product quality requirements. Due to its scalability, membrane filtration is suitable for both small and large-scale applications, making it a versatile solution tailored to specific needs.
Microfiltration is the initial step, used to clarify the solution by removing cell mass, suspended solids, bacteria, and larger macromolecules. By eliminating these larger contaminants, the solution is better prepared for further refinement.
Ultrafiltration is then employed to concentrate molecules and remove smaller contaminants that the MF membrane cannot reject. By reducing the burden on downstream processes, UF extends the runtime and useful life of the operation, delivering significant operational value.
To achieve the highest level of purity, nanofiltration is the final step in the process. NF technology removes unwanted salts, separates organic molecules from the target product, and purifies the final molecule, ensuring the highest quality. By delivering consistent product quality, these fermentation-derived products can increasingly replace synthetic molecules in industries such as textiles, cosmetics, coatings, urethanes, resins, plastics, and bio-based packaging materials.
How Solecta Can Assist
Selecting the optimal membrane solution can be challenging due to factors such as process conditions, molecular size, pore size, pressure and temperature limitations, and footprint constraints. Solecta can help you choose the right separation strategy and membrane sequence to meet your unique needs and enhance your process efficiency.
At Solecta, our expertise in fermentation applications enables us to help you optimize your separation process for your particular needs – improving membrane lifetime and performance while reducing downtime due to cleaning. This not only enhances purification and increases productivity but lowers your total cost of operation.
As sustainability becomes a core value for companies worldwide, optimizing fermentation processes to improve yields and reduce environmental impact is increasingly important. With membrane filtration, you can achieve greater selectivity, increased productivity, and enhanced purification, maximizing the yield and profitability of your operations.
Related Resources in the Knowledge Hub
Let’s Keep in Touch
Follow Solecta on LinkedIn and join our mailing list to keep up with our latest news.
Explore the Possibilities
Our team of application engineers and domain experts understands your industry’s unique challenges. (They’re also eager to solve them.)