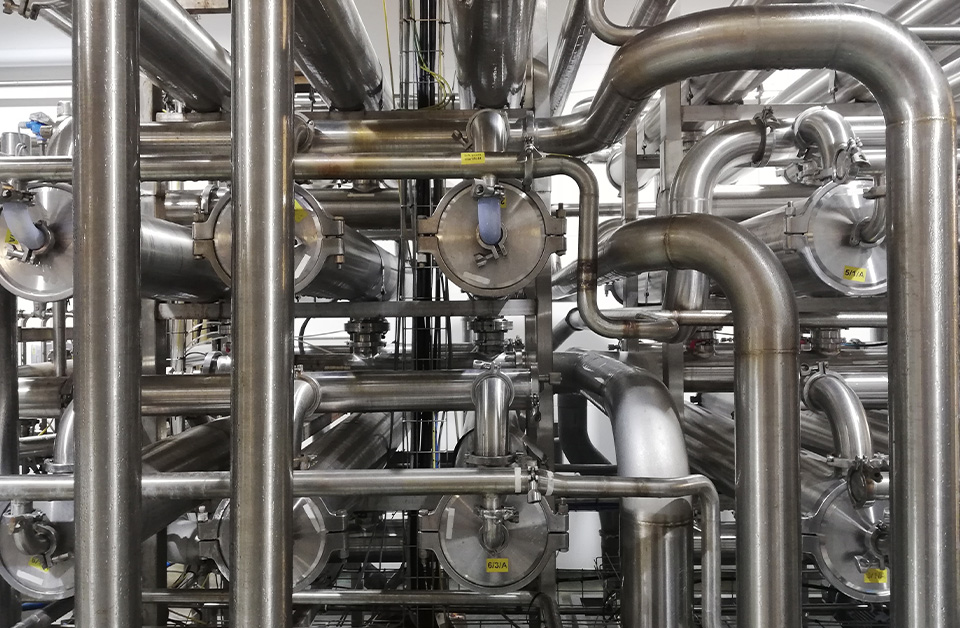
Seamless Solutions: The Benefits of Integrating Spiral-Wound Membranes into Food Manufacturing Processes
In the fast-paced world of food manufacturing, achieving success requires staying ahead of the curve. Embracing innovative technologies can provide a competitive edge, and one such approach is the integration of spiral-wound membranes into existing processing operations. Innovative membrane separation systems offer a variety of benefits, ranging from improving product quality to reduced waste and energy consumption. This blog post will delve into spiral-wound membranes, exploring their technology, advantages, and how Solecta has helped food manufacturers seamlessly integrate them into their processes for enhanced efficiency, sustainability and product excellence.
Understanding Spiral-Wound Membranes
Spiral-wound membranes are revolutionizing the food manufacturing industry with their unique design. These membranes efficiently separate and concentrate components in liquid streams through their advanced structure, which allows precise control over the separation process. This ensures the retention of essential components and the removal of unwanted substances. A prime example of their application is whey processing, where ultrafiltration membranes concentrate whey proteins while removing unwanted lactose, salts and other minerals. The success of spiral-wound membranes relies on carefully selected materials of construction that offer high mechanical and chemical stability. Additionally, their spiral configuration optimizes surface area, improving mass transfer efficiency and more effective separations.
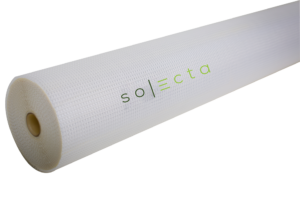
These membranes find use in a range of separation applications, including microfiltration, ultrafiltration, nanofiltration and reverse osmosis, where specific molecules are separated based on size, charge or other characteristics. By selectively removing unwanted components, spiral-wound membranes help to ensure consistent product quality that meets consumer demands and industry standards with each batch. Compared to other traditional separation methods, spiral-wound membranes operate at lower temperatures, reducing energy consumption and operational costs. This heightened efficiency leads to a more sustainable and economically viable manufacturing process. Additionally, these membranes enable the recovery of valuable components, reducing waste and promoting a circular economy within the food industry. This increased sustainability aligns with consumer expectations for environmentally conscious products.
Membrane separation also provides a reliable and efficient method for removing contaminants and potential allergens, ensuring food products meet stringent food safety regulations and standards. Moreover, one of the significant advantages of using spiral-wound membranes is their ease of integration into existing manufacturing processes.
At Solecta, we understand that selecting the optimal membrane technology for a specific application and maximizing the separation efficiency in a given process can be complex and challenging. Therefore, we collaborate closely with our clients to analyze their operations and identify areas where spiral-wound membranes can deliver the best result and how to implement them effectively. Following a thorough analysis of the process objectives, our team of experts provides customized membrane solutions that seamlessly integrate into existing processes to achieve the desired results.
Process Integration Success and Challenges
The dairy industry has experienced tremendous success by integrating spiral-wound membranes into milk and whey processing, leading to improved product quality and optimized resource utilization. One such application involves ultrafiltration to concentrate liquid whey protein isolate before spray drying. While achieving this with a protein evaporator is possible, the high heat applied may adversely affect the final protein product, causing unwanted denaturation or changes in color. Alongside enhanced product quality and consistency, numerous dairy and other food industry manufacturers have reported significant cost savings, increased productivity and improved yield after implementing spiral-wound membranes, highlighting the tangible benefits and returns on investment.
To ensure the successful integration of spiral-wound membranes into food manufacturing processes, conducting a comprehensive evaluation with a knowledgeable partner like Solecta is important. Our team of experts can identify areas in the manufacturing process that could benefit from membrane integration, such as concentration, clarification and purification. Our expertise allows us to customize the highly versatile spiral-wound membranes to suit different food products, ensuring seamless integration without compromising product quality.
During the integration process, risk management plays a pivotal role. Identifying and mitigating potential risks ensures a smooth and successful transition to spiral-wound membrane technology. Two key considerations specific to membrane separation include selecting the appropriate type of filtration for the application, whether reverse osmosis, nanofiltration, ultrafiltration or microfiltration, and fully understanding the capacity needs of the process. Sizing the system appropriately is critical. A system that is too small creates unwanted process bottlenecks, while an oversized system inflates capital costs and results in an underutilized asset. Solecta works closely with clients to mitigate these risks and ensure a smooth transition. Our engineers help size the membrane system appropriately based on our clients’ capacity needs. Through pilot testing and simulation, we overcome integration challenges to deliver a solution that exceeds our client’s expectations.
Embracing the Future
Continued research and development in membrane materials and designs hold the potential for even greater efficiency and applicability in the food industry. As membrane technology advances, new applications will emerge, further expanding the benefits of spiral-wound membranes. Integrating these membranes into existing food manufacturing processes presents a transformative opportunity for the industry. By embracing this technology, companies can stay at the forefront of sustainability and regulatory compliance while improving product quality and efficiency.
Solecta can help you understand the benefits of utilizing membrane technology to achieve your business objectives, assess critical integration points, and mitigate potential risks to unlock the full capability of membrane separation systems for your process. The seamless integration of spiral-wound membranes holds the power to transform food manufacturing, setting the stage for a brighter and more sustainable future for the industry.
Let us help you explore membrane separation solutions and experience the positive impact on efficiency, sustainability, and product quality this technology brings to your operations.
Related Resources in the Knowledge Hub
Let’s Keep in Touch
Follow Solecta on LinkedIn and join our mailing list to keep up with our latest news.
Explore the Possibilities
Our team of application engineers and domain experts understands your industry’s unique challenges. (They’re also eager to solve them.)